How Do We Ensure Top-Notch Gauze Quality and Timely Delivery?
In the medical supplies industry, particularly for essential products like gauze, maintaining a high standard of quality while ensuring timely delivery is a crucial balancing act. As the CEO of banghaoningmed, I’ve navigated these challenges firsthand, and I’m here to share some insights into how we achieve this delicate balance.
The cornerstone of our approach at banghaoningmed is a rigorous quality control system coupled with efficient supply chain management. By controlling production from weaving to packaging, we ensure that each gauze roll, bandage, and swab meets the highest standards.
But how do we maintain this consistency in quality? It starts right at the source. Our own weaving and dyeing factories play a pivotal role. By overseeing the entire production process, we can promptly address any quality issues that arise.
How Important is Quality Control in Gauze Production?
Quality control in medical supplies is not just about meeting standards; it’s about safeguarding lives. In our factories, quality checks are conducted at every stage of production. From raw materials to finished products, each item is scrutinized to ensure it meets both international and industry-specific standards .
How Does Supply Chain Management Affect Delivery Times?
Efficient supply chain management is the backbone of timely delivery.
Our factory maintains a long-term inventory of 100 tons of cotton yarn. Once the order is confirmed, we can immediately start spinning, weaving, weaving, cutting finished products, and packaging. Our production process significantly shortens the waiting time for raw materials.
In addition, we have more than a dozen automated production lines, and the machines can work 24 hours a day.
Our prices for abdominal pad products are the lowest in China. We have more than 200 high-quality and skilled sewing workers to ensure delivery.
What Role Does Technology Play in Ensuring Quality and Delivery?
The key is to adopt the latest high-end equipment technology. High-end equipment is fully automated and reduces manual participation. It is fast and less error-prone, ensuring quality and delivery time to a large extent.
How Do We Handle Unexpected Supply Chain Disruptions?
In today’s volatile market, it’s crucial to have contingency plans for supply chain disruptions. At Banghaoningmed, we maintain strong relationships with multiple suppliers and logistics partners. This network allows us to pivot quickly in case of any unforeseen circumstances, ensuring minimal impact on delivery schedules
Can Customization Impact Quality and Delivery?
Customization is a significant aspect of our business model. While it presents challenges, we’ve streamlined our processes to handle customized orders without compromising on quality or delivery time. Our flexible manufacturing system allows us to adapt to unique client requirements efficiently .
Why is Client Communication Integral to Our Process?
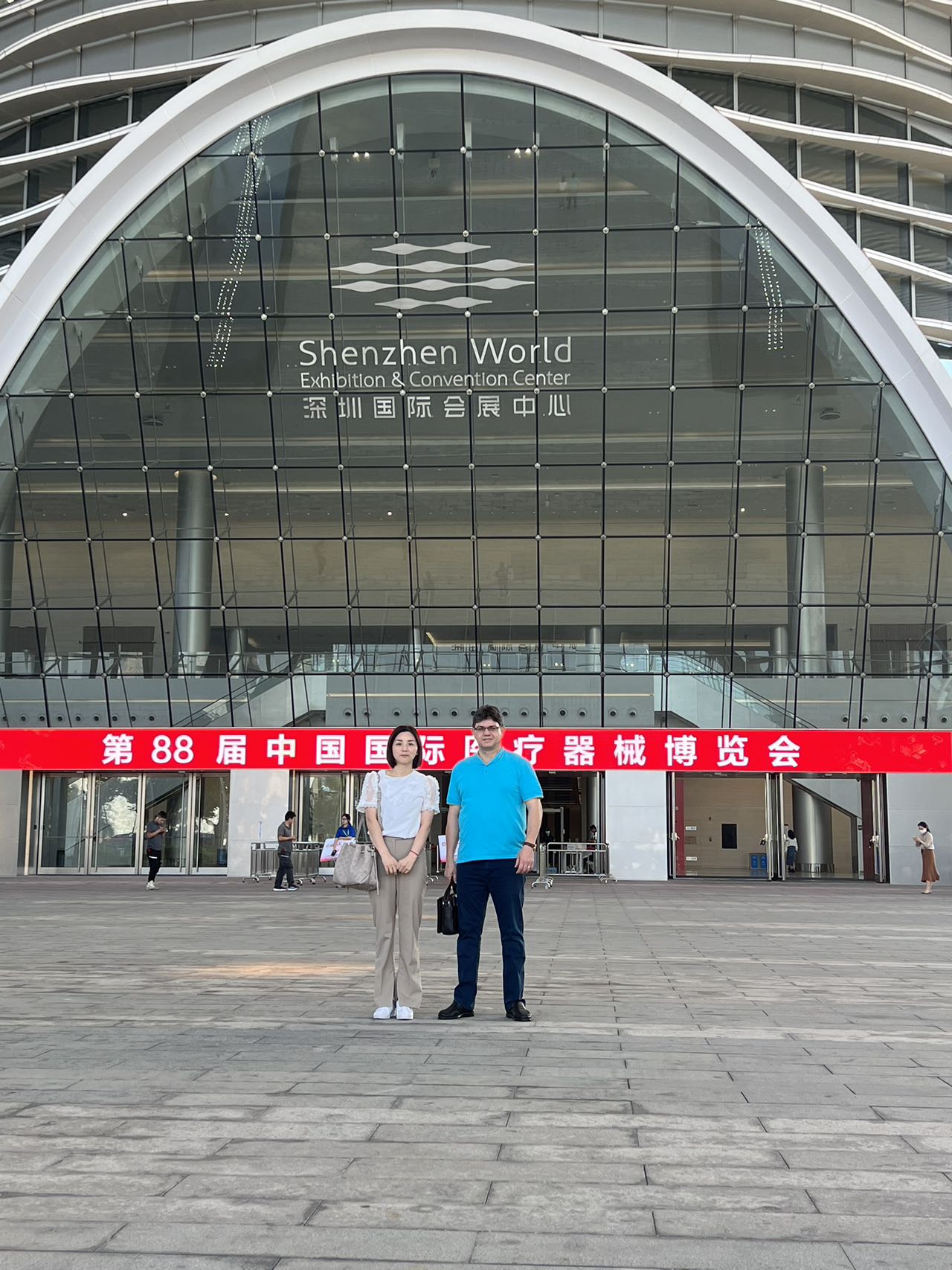
Open and continuous communication with clients is essential. It helps in understanding their needs better and also in providing timely updates about their orders. This transparency builds trust and ensures that any potential issues are addressed proactively .
Conclusion
At Banghaoningmed, our commitment to quality and timely delivery is unwavering. We understand that in the healthcare industry, these factors can mean the difference between life and death. That’s why we are constantly evolving and improving our processes to serve our clients better. The journey isn’t always smooth, but our dedication to excellence remains steadfast.